Micro Arc Oxydation (MAO)
Qu'est ce que la Micro Arc Oxydation ?
Appellations: MICRO ARC OXIDATION, MICRO PLASMA, ELECTRO PLASMA, MAO, OMA…
Introduction
Depuis 1857, on sait qu’un film protecteur d’oxyde se forme sur une anode en aluminium dans une cellule d’électrolyse de l’eau ; c’est le principe de « l’oxydation anodique », Lors d’un procédé d’anodisation, il ne se forme généralement pas de décharges électriques.
Bien que les phénomènes de décharge électrique se produisant dans les électrolytes aient été découverts il y a plus de 120 ans, il faut attendre 1932 pour que Güntherschulze et Betz en proposent une application: le dépôt anodique par étincelage. L’exploitation des plasmas électrolytiques, dans le domaine des traitements de surface, n’a réellement été entreprise que dans les années 1960 par Mc Neill et Gruss.
En 1967, Wood et Pearson établissent le lien entre la tension de claquage, le type d’éléments d’alliage pour un métal donné et la concentration des constituants de l’électrolyte.
En 1970, Yahalom et Hoar montrent que l’augmentation de tension observée au début du traitement est d’autant plus rapide que la densité de courant imposée est grande. En revanche, ils établissent que la tension de claquage est indépendante de la densité de courant. En 1971, Yahalom et Zahavi regroupent les différents résultats obtenus au cours des années précédentes et en déduisent que le claquage est contrôlé à l’interface du film électrolyte plutôt qu’au cœur de la couche d’oxyde.
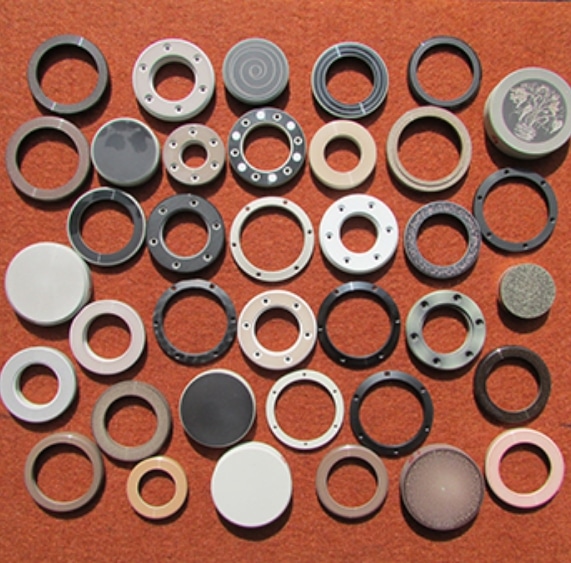
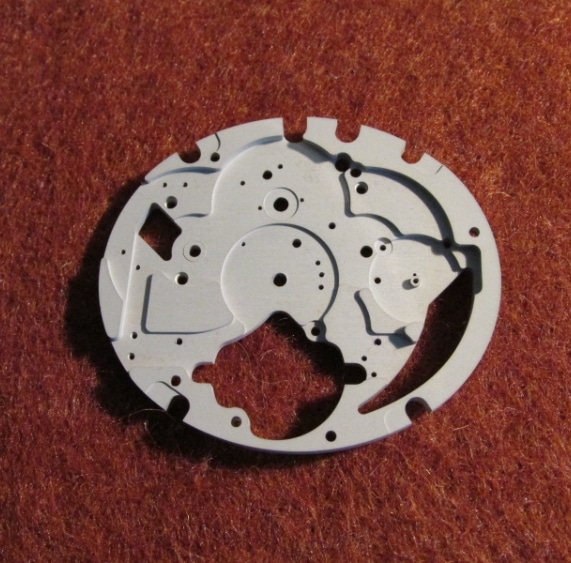
Pendant la même période, Brown et ses collaborateurs montrent que si l’on maintient une tension constante pendant le traitement, l’intensité du courant diminue à mesure que la résistivité de la couche d’oxyde augmente jusqu’à extinction de la décharge. C’est pour cette raison qu’en 1976, Markov et ses collaborateurs augmentent la tension pendant le traitement pour maintenir une densité de courant suffisante, éviter l’extinction de la décharge et ainsi permettre la poursuite de la croissance du film d’oxyde.
Des études plus approfondies ont été mises en place depuis la fin des années 70. Outre la qualité des couches obtenues, l’oxydation par plasma électrolytique présente l’avantage d’être un procédé propre.
Le procédé d’oxydation micro-arcs permet de transformer la surface de l’aluminium en céramique dure, le revêtement élaboré possède des propriétés inégalées.
Respect de l’environnement grâce à l’utilisation d’un électrolyte écologique.
Possibilité de traiter toutes les nuances d’alliages d’aluminium, il en résulte de nombreuses teintes.
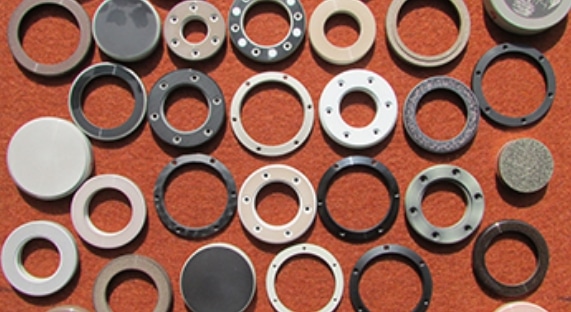
Possibilité de réaliser des couches fines ou épaisses de 1 à 150 µm, le contrôle de l’épaisseur des couches est effectuée à l’aide d’un appareil à courant Foucault avec une précision de l’ordre d’environ 2 µm.
La dureté: environ 10 fois supérieure à celle de l’alliage de base.
Résistance à la corrosion: de 500 à 3000 heures d’exposition au brouillard salin.
Résistance à la sueur synthétique: exposition à 36° de 150 à 300 heures pour l’alliage de la série 2000, pour les series 1000 ; 4000 ; 5000 ; 6000 la tenue est supèrieure à 500 heures.
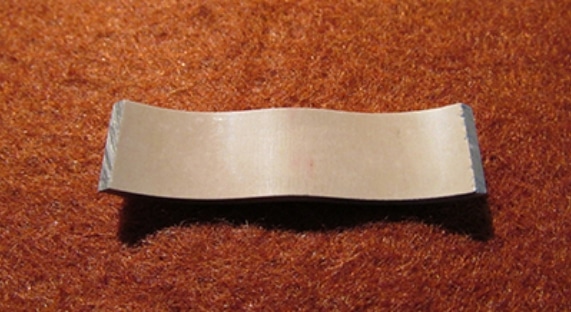
Resistance à l’arrachement: forte adhérence de la couche céramique, résiste aux chocs thermiques et aux déformations géométriques, comme le montre le test sur l’image ci-dessous, un bout de cylindre à qui l’on a fait subir une déformation, le constat montre que la couche ne s’est pas décrochée du substrat mais s’est fissurée du fait de sa dureté élevée.
Traitement à température ambiante :
- Pas de déformation des pièces traitées
- Pas de modification métallurgique de l’alliage
Possibilité de traiter des pièces de géométrie complexe et de réaliser des épargnes
La finition: est obtenue par un procédé de honage, (appellation plus commune le rôdage), la couche va subir un important changement de la diminution de la partie poreuse a la couche dense, gras au passage d’un rodoir a multi pierre en diamant, qui permettra d’obtenir atteindre des rugosités inférieures à 0,03 µm avec des précisions dimensionnelles de l’ordre du micron.
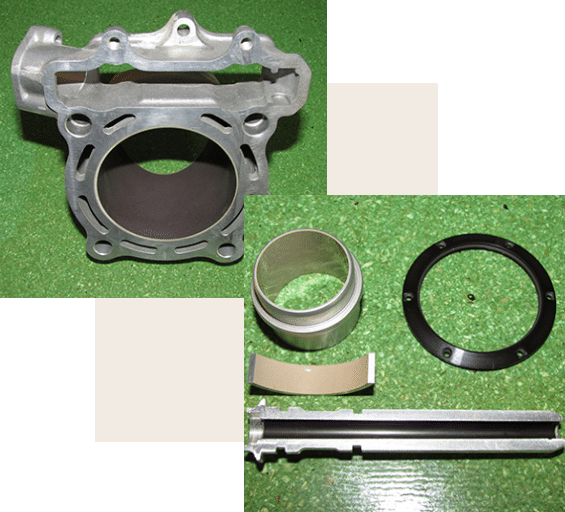
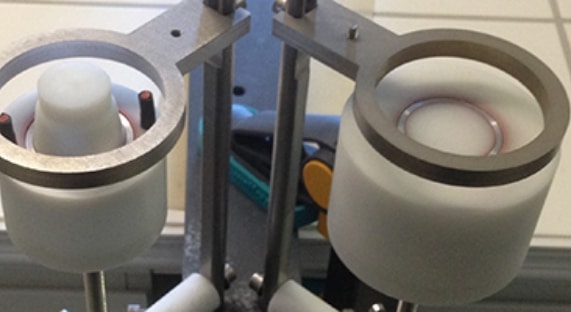
La société MTG est spécialisée dans le traitement de surface des alliages légers par oxydation micro-arcs (OMA). Le procédé d’oxydation micro-arcs permet de transformer la surface d’alliages légers en céramique dure.
L’oxydation de la surface des pièces en alliages d’aluminium, magnésium et titane s’obtient dans un bain à base aqueuse, sans aucune pollution pour l’environnement. La parfaite maîtrise des courants alternatifs et des électrolytes permet notamment d’optimiser le temps de traitement et l’élaboration de couches diverses sur un même alliage.
Les revêtements céramique obtenus, d’une épaisseur comprise entre 50 à 120 microns, se distinguent par d’excellentes propriétés physiques telles que la dureté, la résistance à l’usure, l’adhérence et la résistance à la corrosion.
Pour des applications exigeant un faible coefficient de frottement, il est possible de rectifier, polir, honer les couches de manière à éliminer la couche poreuse de surface et atteindre la couche dense, avec une rugosité qui peut être inférieure à 0,03 µm et une tolérance dimensionnelle pouvant atteindre l’ordre du micron.
Propriétés des couches
La couche croît de part et d’autre de la surface initiale du substrat environ 50% vers l’extérieur et 50% vers l’intérieur.
Observation en microscopie électronique à balayage en coupe transversale.
La couche est constituée d’une couche dense (côté substrat) et d’une couche poreuse. Le traitement MAO permet d’élaborer des couches d’épaisseur variant entre 1 et 150 µm.
Substrat : alliage d’aluminium à l’aide d’un microscope électronique à balayage couplé à un système d’analyse par dispersion d’énergie:
Les analyses de surfaces mettent en évidence la présence majoritaire des éléments aluminium et oxygène ainsi que celles du silicium et du potassium (provenant de l’électrolyte). On note en outre la présence en surface d’éléments d’alliages tels que le cuivre, le zinc et le magnésium.
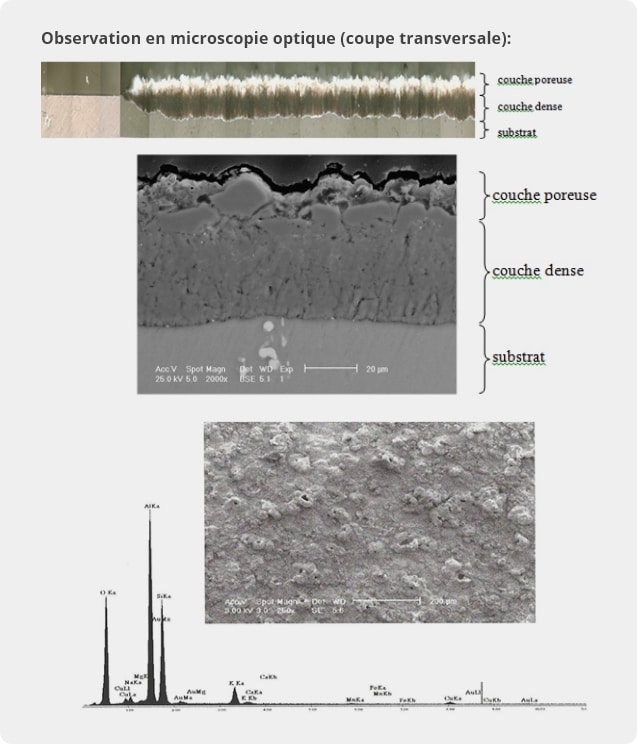
Le procédé MAO permet de faire varier la fréquence électrique, ce paramètre joue un rôle prépondérant sur la porosité des couches obtenues, comme le montrent les micrographies MEB présentées ci-dessous, correspondant à des couches élaborées à des fréquences de 100 Hz (à gauche) et de 500 Hz (à droite).
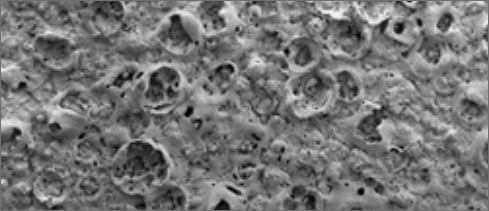
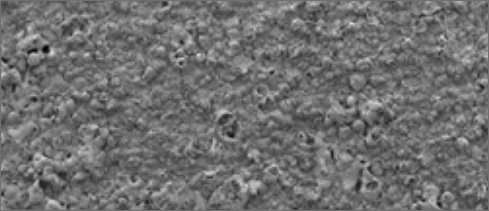
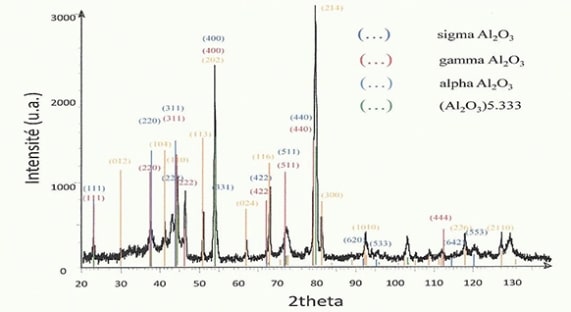
Résistance à la corrosion
Les durées d’exposition en brouillard salin (ISO 9227) sans apparition de piqûres de corrosion ont pû atteindre de 1000 à 3500 heures sur 7175 T73 pour différentes conditions de traitements et des épaisseurs de revêtement brut de 60 à 100 microns d’épaisseur et 500 heures sur AU5NKZr pour 120 microns d’épaisseur.
Dureté de la couche dense
La dureté de la couche dense est environ 10 fois supérieure à celle de l’alliage de base.
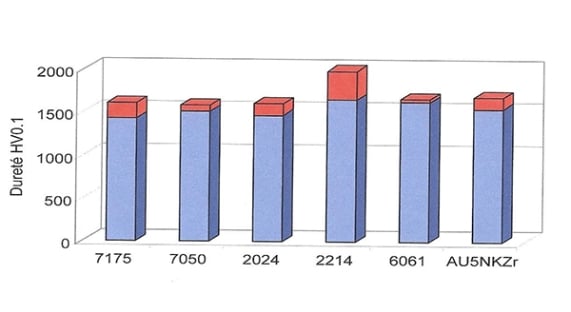
Adhérence
Les essais d’adhérence conventionnelle sont difficilement applicables à ces revêtements. Aussi, des tests de chocs thermiques par refroidissement rapide (250°C 20°C) ont été réalisés. Aucune détérioration des revêtements n’a été observée.
Caractéristiques tribologiques
Les revêtements présentent de très bonnes propriétés de résistance à l’usure (frottement à sec, abrasion…). En particulier, les résultats d’essais Taber présentés ci-après indiquent que la couche dense résiste extrêmement bien à l’abrasion.
Au début de l’essai, on observe une perte de masse importante, due à l’usure de la couche poreuse. La perte de masse diminue fortement lorsque l’on atteint la couche dense. Si la pièce est rectifiée avant l’essai, il n’y a quasiment aucune perte de masse durant tout l’essai comme le montre la courbe bleue. Les photographies ci-dessous présentent l’aspect de l’échantillon et de la couche coupe transverse avant et après l’essai.
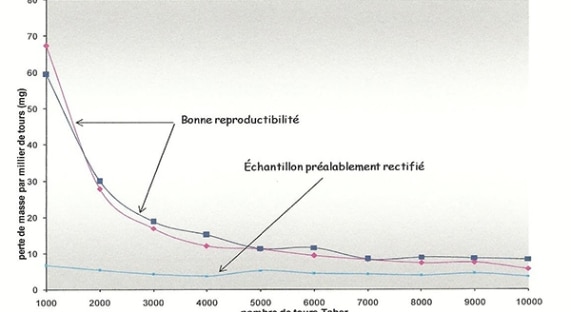
Rectification des couches
Il est possible de limiter fortement le coefficient de frottement par rectification des revêtements MAO. Les couches réalisées avec le traitement MAO atteignent ainsi des rugosités inférieures à 0,03 µm, comme le montre la micrographie suivante, réalisée par microscopie électronique à balayage (grandissement x 100000).
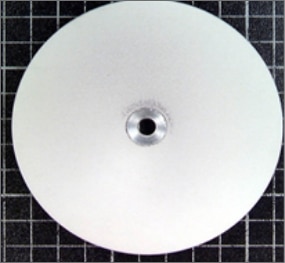
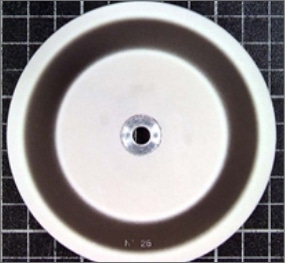
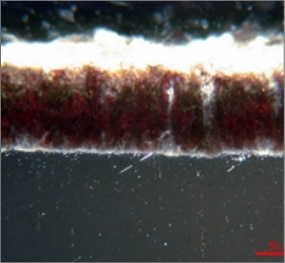
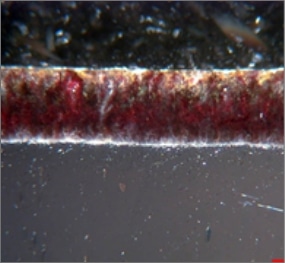
Dans les cas où la rectification des couches est nécessaire, la possibilité de faire croître des couches d’épaisseur supérieure à 90µm sera favorable à l’obtention de cotes précises de l’ordre du micron.
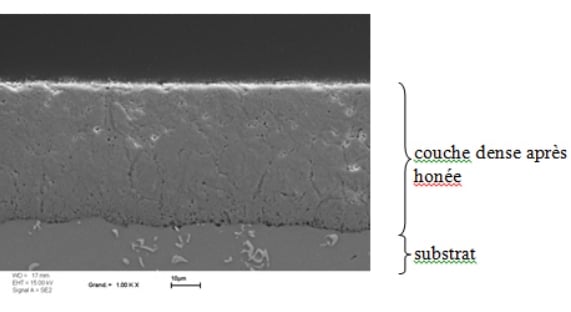
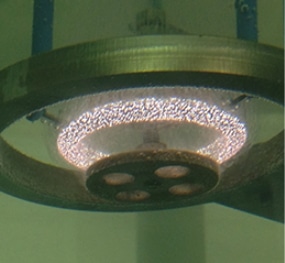
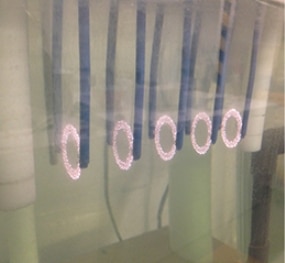
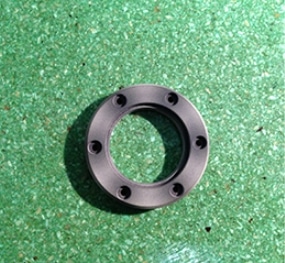
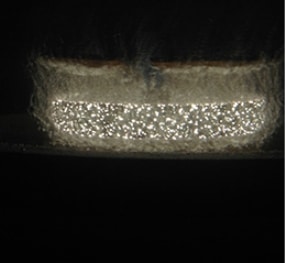
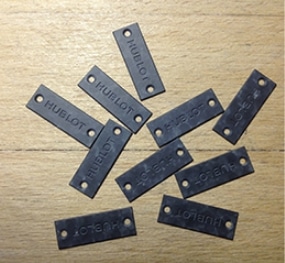
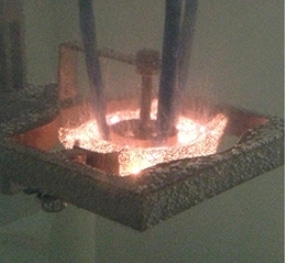
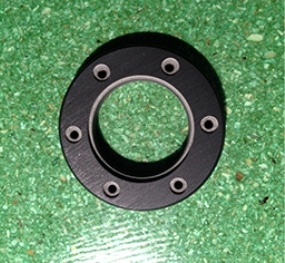
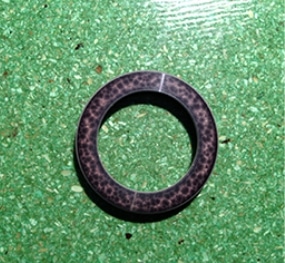